How Marine & Offshore Lighting Demands Dual Explosion/Flame Proof Compliance
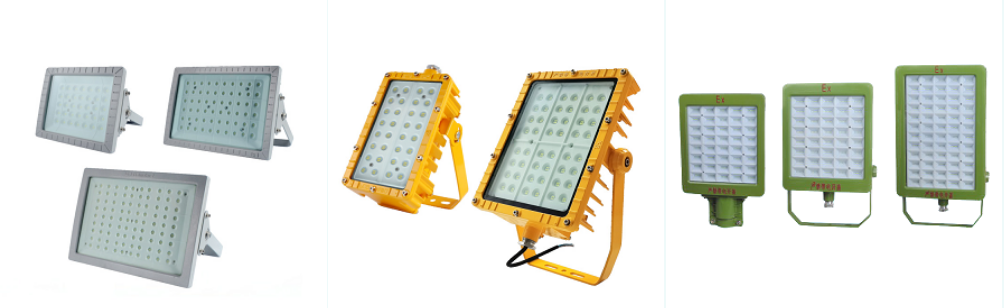
Navigating Safety and Certification Challenges in High-Risk Maritime Environments
Introduction: The Unique Risks of Marine and Offshore Lighting
Marine and offshore environments—such as oil rigs, cargo ships, and LNG carriers—face unparalleled safety challenges due to constant exposure to flammable gases, corrosive saltwater, and explosive dust.
Explosion/Flame Proof: Traditional explosion-proof (Ex d) or flame-proof (FLP) lighting systems alone often fall short in these settings, where dual compliance with explosion containment and flame resistance standards is non-negotiable.
This article explores the technical, regulatory, and operational imperatives driving the adoption of dual-certified lighting solutions in maritime industries.
1. Environmental Challenges Driving Dual Compliance
A. Combustible Atmospheres
Offshore platforms and ship engine rooms frequently encounter methane, hydrogen sulfide, and hydrocarbon vapors. Lighting fixtures must prevent internal explosions (Ex d) while resisting external ignition from nearby leaks.
Case Study: A 2024 incident on a North Sea rig highlighted how non-FLP-certified LED housings ignited external gas clouds despite passing Ex d pressure tests.
B. Corrosive and Dynamic Conditions
Saltwater corrosion degrades traditional aluminum enclosures, compromising flame paths. Dual-compliant systems use stainless steel with ceramic coatings to maintain IP66 ratings and flame arrestor integrity in marine environments.
Vibration from ship engines and waves demands shock-resistant designs, such as GRP (glass-reinforced plastic) housings tested to IEC 60079-31 for mechanical durability.
2. Certification Gaps and Regional Standards: Explosion/Flame Proof
A. ATEX vs. Marine-Specific Certifications
ATEX/IECEx: Mandate dual testing for Zone 1 (gas) and Zone 21 (dust) compliance, but lack specific protocols for saltwater exposure.
Marine Certifications: CCS (China Classification Society) and IMO (International Maritime Organization) require dual Ex d/FLP compliance with enhanced corrosion resistance, as seen in Hi-Sea Marine’s LED fixtures certified for offshore drilling platforms.
B. North American Shortcomings
NEC Division 1 focuses on explosion containment but neglects flame propagation risks in Zone 22 dust environments. Hybrid solutions combining UL 844 and IP66 sealing are critical for cargo ships transporting grain or coal.
3. Engineering Innovations for Dual Compliance
A. Material Breakthroughs
Nano-Ceramic Coatings: Applied to stainless steel housings, these reduce heat transfer by 35% and withstand temperatures up to 800°C, preventing external ignition in LNG storage zones.
Conductive Epoxy Seals: Eliminate static sparks in methane-rich environments while resisting saltwater degradation, crucial for coal carriers and oil tankers.
B. Modular and IoT-Enabled Designs
Replaceable Flame Arrestors: Allow onboard maintenance without disassembling fixtures, reducing downtime in offshore wind farms.
Thermal Sensors: Integrated into LED drivers, these monitor enclosure integrity and trigger shutdowns if temperatures exceed 85°C, aligning with IEC 60079-17 maintenance protocols.
4. Operational and Maintenance Strategies
A. Cost-Effective Compliance
Dual-certified fixtures incur 20–30% higher upfront costs than single-standard models but reduce retrofit expenses in global fleets. For example, a VLCC (Very Large Crude Carrier) saved $120,000/year by avoiding region-specific lighting replacements.
B. Predictive Maintenance
Infrared Thermography: Quarterly scans detect delamination in flame-retardant layers, a common failure point in humid marine environments.
Torque Calibration: Annual checks on Ex d enclosures ensure bolt tensions remain within ±10% of ISA 60079-17 specifications, preventing pressure leaks.
5. Future Trends: Sustainability and Smart Integration
A. Bio-Based Flame Retardants
Lignin-derived additives replace toxic brominated compounds, complying with EU REACH regulations and reducing disposal costs in decommissioned offshore platforms.
B. Digital Twins for Certification
Virtual simulations predict fixture performance under extreme conditions (e.g., -40°C Arctic operations), cutting physical testing costs by 40%.